C-Frame Roll Measurement
Maximum Efficiency and High-Precision Roll Grinding
The C-frame calipers are high-precision devices for measuring rolls.Thanks to their compact and robust design featuring swivelling arms, the calipers are suited for very small as well as for very big roll diameters.
Benefits:
- The measurements are absolute - no interpolation based on a single measuring point!
- Two-point measurement possible during the grinding process
- 100% grinding history for tracking and optimization
- Measurement results and corrections “on the fly” during the process
- Industrial diamond touch probes - no scratch marks on the roller surface!
- 3-point measurement of the roller position via C-frame and C-probe
Roll Inspection – Eddy Current & Ultrasonic
Early Detection of Roll Defects
Eddy Current measuring reliably locates open cracks and changes in the roll texture. Since the Eddy Current sensor is integrated in the roll measuring system, all measurements are carried out during grinding and therefore without delay. Manufacturing defects within the roll as well as fatigue from operation in the mill are detected during a separately running ultrasonic inspection.
Benefits:
- Ultra-fast data exchange - diagnosis in real time
- Measuring "on the fly" during the grinding process
- Integrated and fully automatic
- Early detection of roll defects
- Full integration into the control system
- Downtimes are effectively minimized
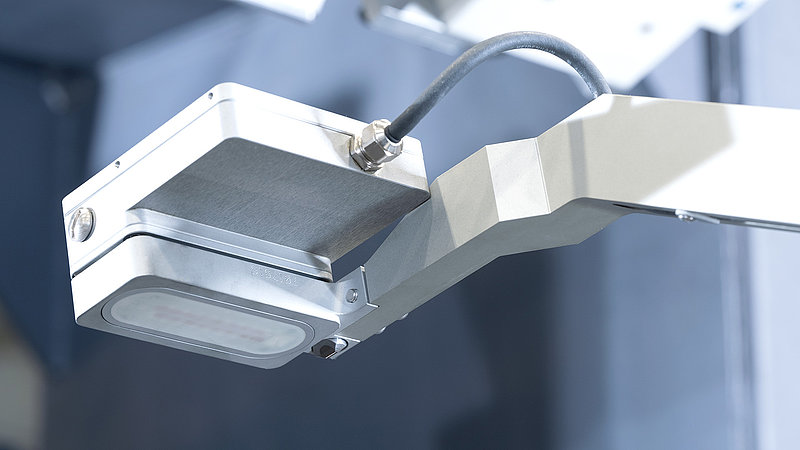
Surface Inspection – Roll Surface Inspection System (RSIS)
Reliable Monitoring of the Roll Surface
For the automatic detection of roll surface defects, HCC/KPM offers the laser measuring device Roll Surface Inspection System (RSIS). In the post-process, RSIS records and evaluates the reflexion of a laser beam on the roll surface. Machining errors, such as chatter and infeed marks, commas, clouds and similar defects are reliably detected.
Benefits:
- Detects all types of optical defects on the roller surface
- Tracking: Errors caused by faulty roll grinding can be traced thanks to the RSIS measurement logs.
- Automatic quality control regardless of the operator's experience
- Ensuring the repeatability of quality
- Consistently high roll throughput
- Full integration into the control system

Surface Roughness via Scattered Light - Roughness Scattered Light Detection (RSLD)
Optical Measuring Method of Highly Sensitive Surfaces
Another innovative technology that Herkules offers for maximum processing efficiency is the Roughness Scattered Light Detection (RSLD) measuring technology, which determines and documents the surface roughness over the entire roller bale area without contact via scattered light, thus ensuring perfect homogeneity of the roller surface.
Benefits:
- Highly complex and precise evaluation of the roller surface
- Use of the testing technology during the ongoing grinding process
- Output of the surface roughness value (Ra) and the scattered light diffusion value (Aq)
- Non-contact surface inspection
- Measurements in grinding and rolling direction
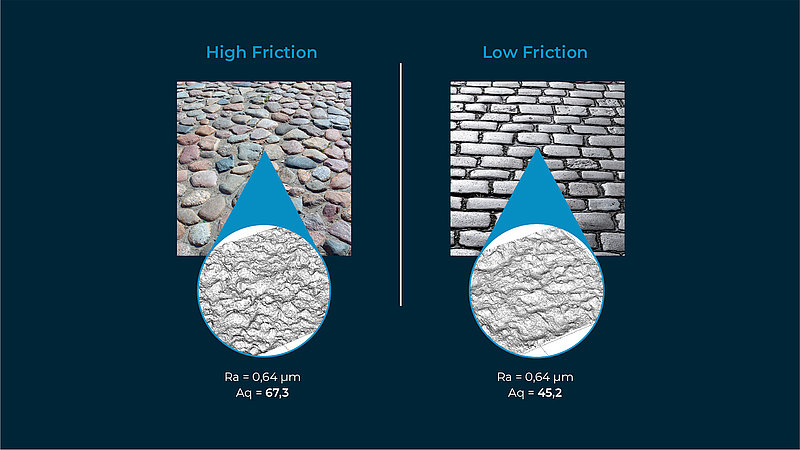