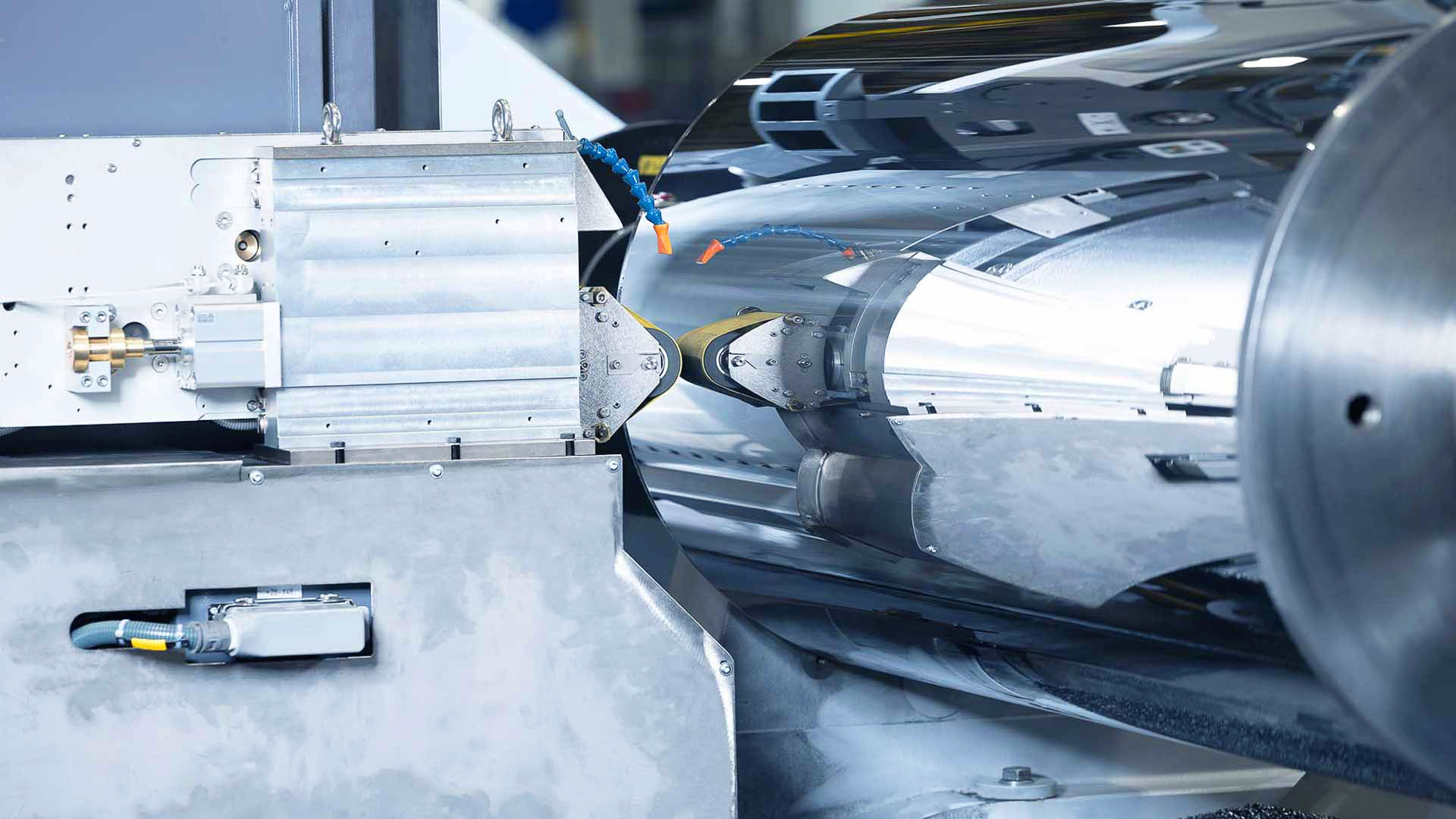
Perfectly Ground Rolls for High Availability and Top Quality
WS 450 KL x 4,500 Convinces American Customer for the Production of Aluminum Products
In the aluminum industry, the highest demands are placed with regard to homogeneity and geometry of roll surfaces. An American customer is once again relying on the top-quality technical products from Maschinenfabrik Herkules and decided to buy a WS 450 KL x 4,500 roll grinding machine to perfectly and reliably grind work rolls for its cold rolling mill for the production of aluminum foil.
Operators of cold rolling mills have been trusting in the proven Herkules technology for decades. The geometric precision of the rolls is the basic prerequisite for the production of high-quality cold strip in the aluminum and steel industries. The high machine rigidity in combination with excellent damping properties constantly guarantees grinding results at the highest quality level. The "on the fly" measuring and grinding process, controlled with the intuitive KP 10 control, ensures significantly shorter processing times and thus higher availability. At the same time, the optimized grinding stock removal increases the service life of the rolls used. To minimize downtimes in the rolling mill, it is important to detect defective rolls at an early stage. Herkules has developed surface inspection technologies that reliably detect cracks and other defects close to the roll surface that are not visible to the naked eye. An eddy current measurement device (Eddy Current) reliably locates cracks and changes within the roll's structure.
The machine comes with patented Monolith™- bed - the superior Herkules technology is manufactured in sandwich design with cast-iron ribbed top section, fiber-reinforced high-performance mineral concrete and a base plate made of steel and special damping elements. Because there is no metallic connection between the bottom and top sections, vibrations are effectively damped. The integration of the workpiece bed and grinding bed into a common machine bed guarantees a consistently accurate alignment even after many years of operation. In addition to that the foundation-free installation directly on the shop floor saves space and costs. The customer has additionally secured himself with an extra service offer, which stands out above all by a fast and reliable spare parts delivery to effectively minimize downtimes ensuring that the customer enjoys the best possible service for decades.
The machine is assembled and installed on site by our experts.
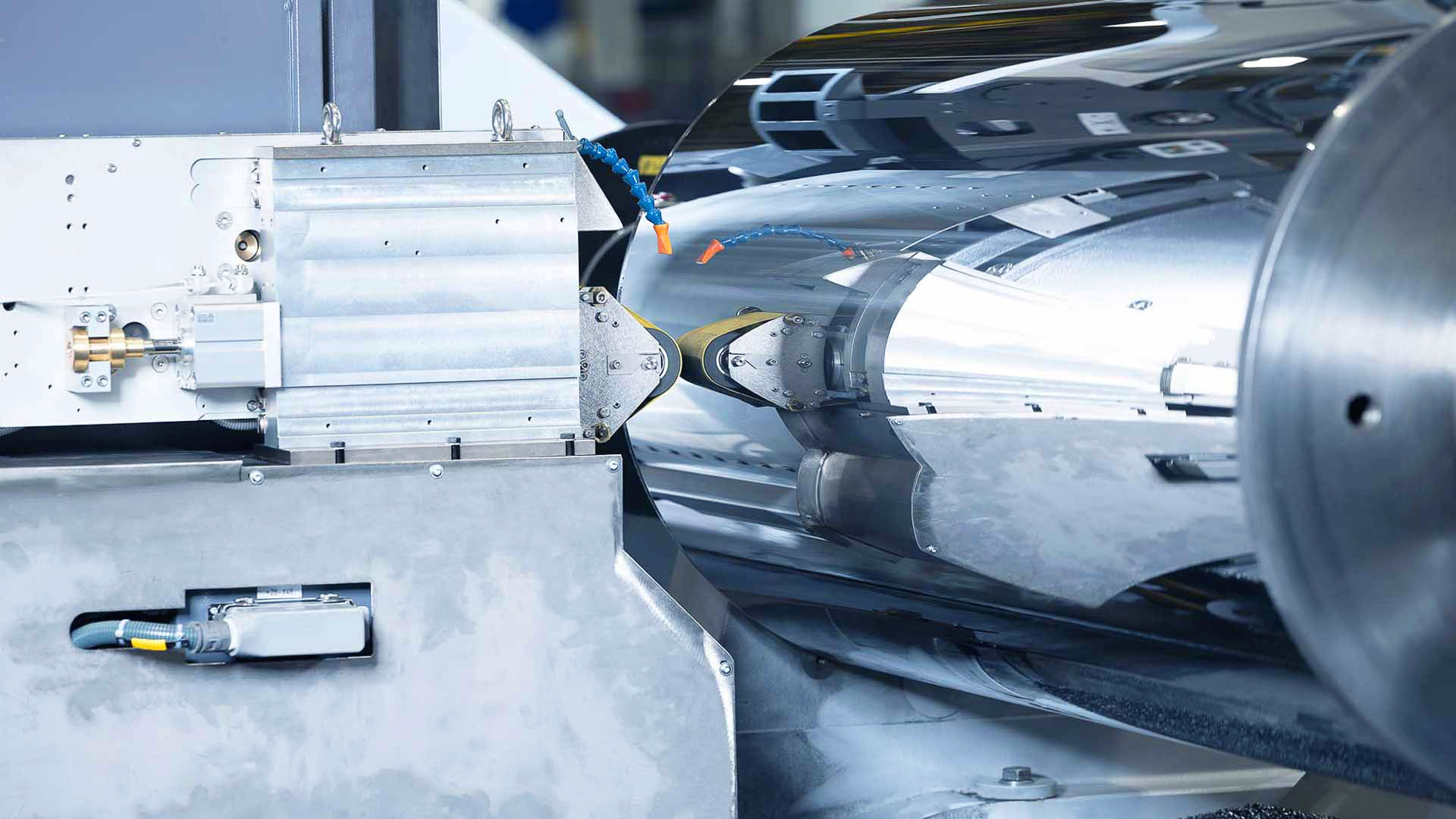
Perfectly Ground Rolls for High Availability and Top Quality
WS 450 KL x 4,500 Convinces American Customer for the Production of Aluminum Products
In the aluminum industry, the highest demands are placed with regard to homogeneity and geometry of roll surfaces. An American customer is once again relying on the top-quality technical products from Maschinenfabrik Herkules and decided to buy a WS 450 KL x 4,500 roll grinding machine to perfectly and reliably grind work rolls for its cold rolling mill for the production of aluminum foil.
Operators of cold rolling mills have been trusting in the proven Herkules technology for decades. The geometric precision of the rolls is the basic prerequisite for the production of high-quality cold strip in the aluminum and steel industries. The high machine rigidity in combination with excellent damping properties constantly guarantees grinding results at the highest quality level. The "on the fly" measuring and grinding process, controlled with the intuitive KP 10 control, ensures significantly shorter processing times and thus higher availability. At the same time, the optimized grinding stock removal increases the service life of the rolls used. To minimize downtimes in the rolling mill, it is important to detect defective rolls at an early stage. Herkules has developed surface inspection technologies that reliably detect cracks and other defects close to the roll surface that are not visible to the naked eye. An eddy current measurement device (Eddy Current) reliably locates cracks and changes within the roll's structure.
The machine comes with patented Monolith™- bed - the superior Herkules technology is manufactured in sandwich design with cast-iron ribbed top section, fiber-reinforced high-performance mineral concrete and a base plate made of steel and special damping elements. Because there is no metallic connection between the bottom and top sections, vibrations are effectively damped. The integration of the workpiece bed and grinding bed into a common machine bed guarantees a consistently accurate alignment even after many years of operation. In addition to that the foundation-free installation directly on the shop floor saves space and costs. The customer has additionally secured himself with an extra service offer, which stands out above all by a fast and reliable spare parts delivery to effectively minimize downtimes ensuring that the customer enjoys the best possible service for decades.
The machine is assembled and installed on site by our experts.