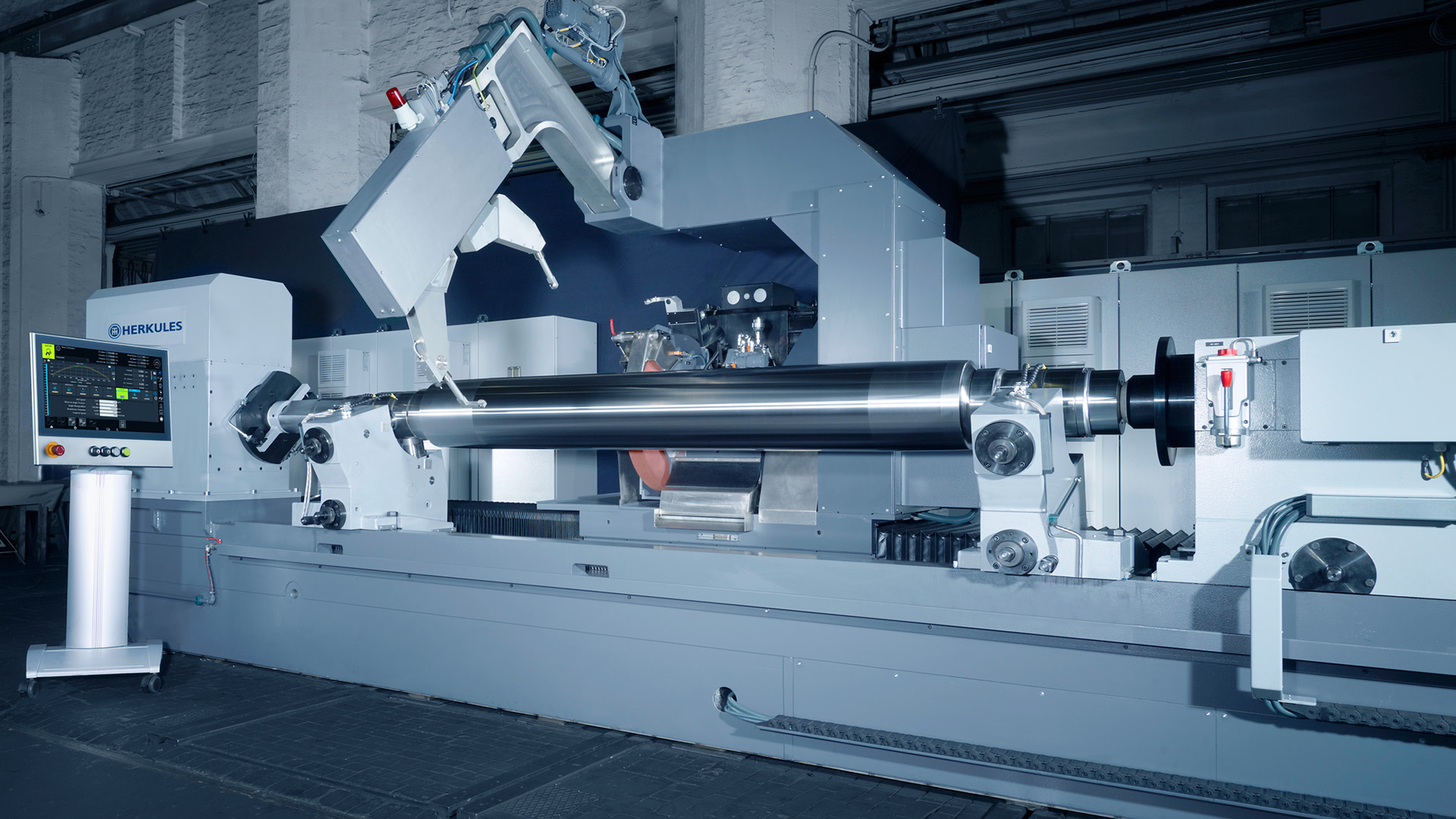
Perfect Rolls, The Very Best Foil
WS 450 AL Monolith™ for Hydro Aluminium Deutschland GmbH
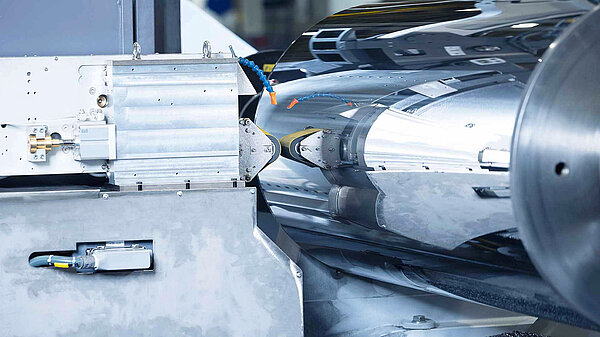
Absolutely accurate roll geometry, exceptional surface quality – the aluminum industry faces ever more demanding requirements. Mills meet these demands with Herkules machines. 90% of all rolls used in foil production are ground with Herkules roll grinders.
Hydro Aluminium Deutschland GmbH has relied on Herkules for many years. In summer 2014 it invested again in a WS 450 AL Monolith™ from the market leader. Hydro Aluminium is a leading global producer of aluminum foil with a thickness of 6 μm and lithography strip with thicknesses of 0.1 to 0.5 mm. The new machine is the fourth Herkules machine at Hydro Aluminium, after a WS 400 and two WS 300 CNC.
Herkules specialists equipped the WS 450 AL Monolith™ with several accessories. It has a HCC/KPM CNC control, developed especially for machining rolls, as well as a HCC/KPM roll measuring system. With its three measuring probes, the roll measuring system allows for highly accurate measuring of the roll geometry and for "correction on the fly". The machine is equipped with a roll surface inspection system (RSIS), which indicates even the minutest surface defects. The Monolith™ design of the grinder saves space and cost. It obviates the need for special machine foundations. It dramatically shortens installation time. The excellent damping characteristics of the vibration absorbing structure bring on a significant improvement in machining accuracy.
The optimal adaptation to the stringent requirements of the aluminum industry makes for accurate and efficient machining – a cornerstone of the customer's competitiveness.
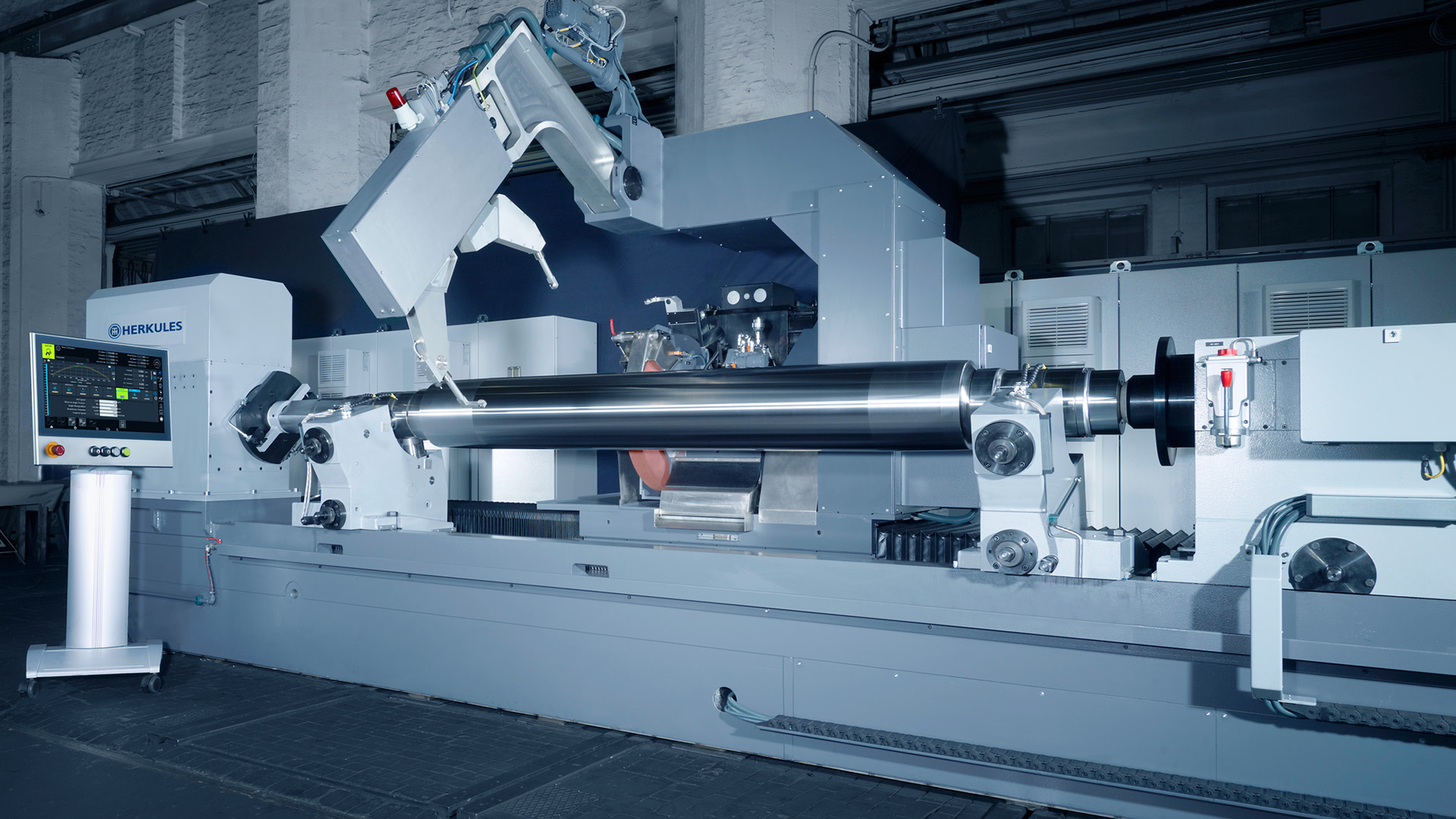
Perfect Rolls, The Very Best Foil
WS 450 AL Monolith™ for Hydro Aluminium Deutschland GmbH
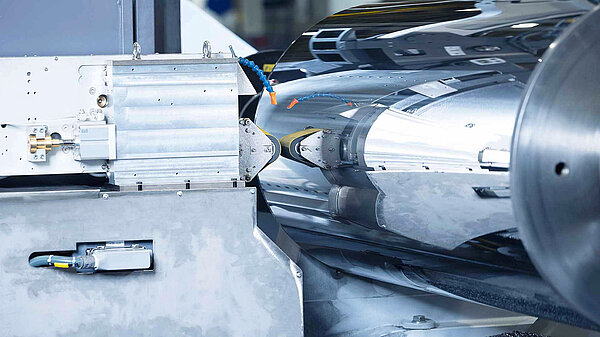
Absolutely accurate roll geometry, exceptional surface quality – the aluminum industry faces ever more demanding requirements. Mills meet these demands with Herkules machines. 90% of all rolls used in foil production are ground with Herkules roll grinders.
Hydro Aluminium Deutschland GmbH has relied on Herkules for many years. In summer 2014 it invested again in a WS 450 AL Monolith™ from the market leader. Hydro Aluminium is a leading global producer of aluminum foil with a thickness of 6 μm and lithography strip with thicknesses of 0.1 to 0.5 mm. The new machine is the fourth Herkules machine at Hydro Aluminium, after a WS 400 and two WS 300 CNC.
Herkules specialists equipped the WS 450 AL Monolith™ with several accessories. It has a HCC/KPM CNC control, developed especially for machining rolls, as well as a HCC/KPM roll measuring system. With its three measuring probes, the roll measuring system allows for highly accurate measuring of the roll geometry and for "correction on the fly". The machine is equipped with a roll surface inspection system (RSIS), which indicates even the minutest surface defects. The Monolith™ design of the grinder saves space and cost. It obviates the need for special machine foundations. It dramatically shortens installation time. The excellent damping characteristics of the vibration absorbing structure bring on a significant improvement in machining accuracy.
The optimal adaptation to the stringent requirements of the aluminum industry makes for accurate and efficient machining – a cornerstone of the customer's competitiveness.
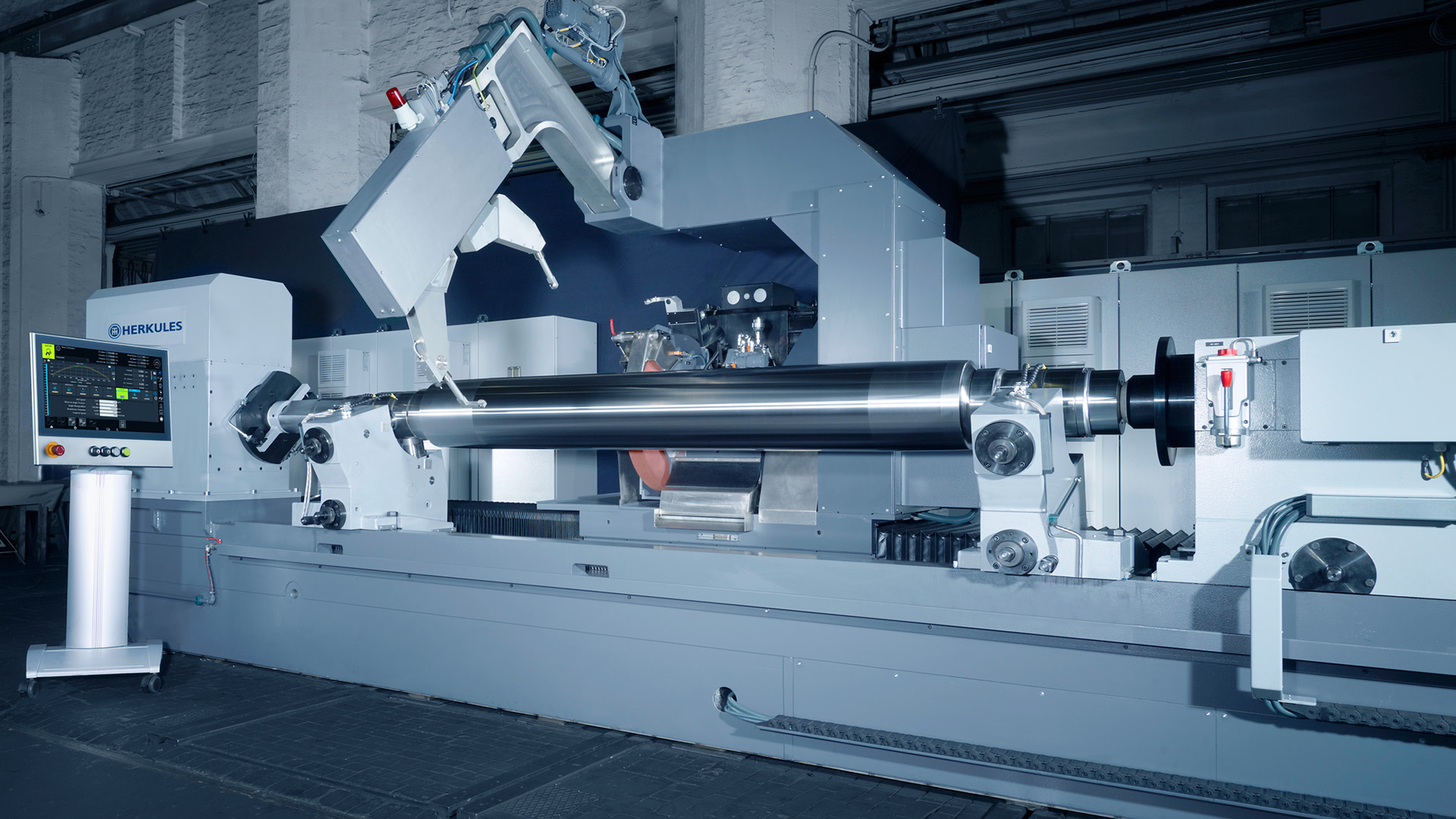
Perfect Rolls, The Very Best Foil
WS 450 AL Monolith™ for Hydro Aluminium Deutschland GmbH
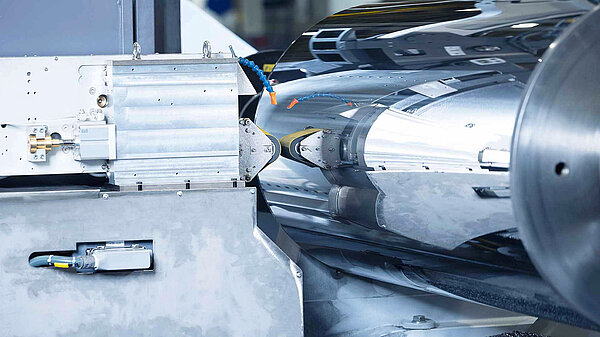
Absolutely accurate roll geometry, exceptional surface quality – the aluminum industry faces ever more demanding requirements. Mills meet these demands with Herkules machines. 90% of all rolls used in foil production are ground with Herkules roll grinders.
Hydro Aluminium Deutschland GmbH has relied on Herkules for many years. In summer 2014 it invested again in a WS 450 AL Monolith™ from the market leader. Hydro Aluminium is a leading global producer of aluminum foil with a thickness of 6 μm and lithography strip with thicknesses of 0.1 to 0.5 mm. The new machine is the fourth Herkules machine at Hydro Aluminium, after a WS 400 and two WS 300 CNC.
Herkules specialists equipped the WS 450 AL Monolith™ with several accessories. It has a HCC/KPM CNC control, developed especially for machining rolls, as well as a HCC/KPM roll measuring system. With its three measuring probes, the roll measuring system allows for highly accurate measuring of the roll geometry and for "correction on the fly". The machine is equipped with a roll surface inspection system (RSIS), which indicates even the minutest surface defects. The Monolith™ design of the grinder saves space and cost. It obviates the need for special machine foundations. It dramatically shortens installation time. The excellent damping characteristics of the vibration absorbing structure bring on a significant improvement in machining accuracy.
The optimal adaptation to the stringent requirements of the aluminum industry makes for accurate and efficient machining – a cornerstone of the customer's competitiveness.
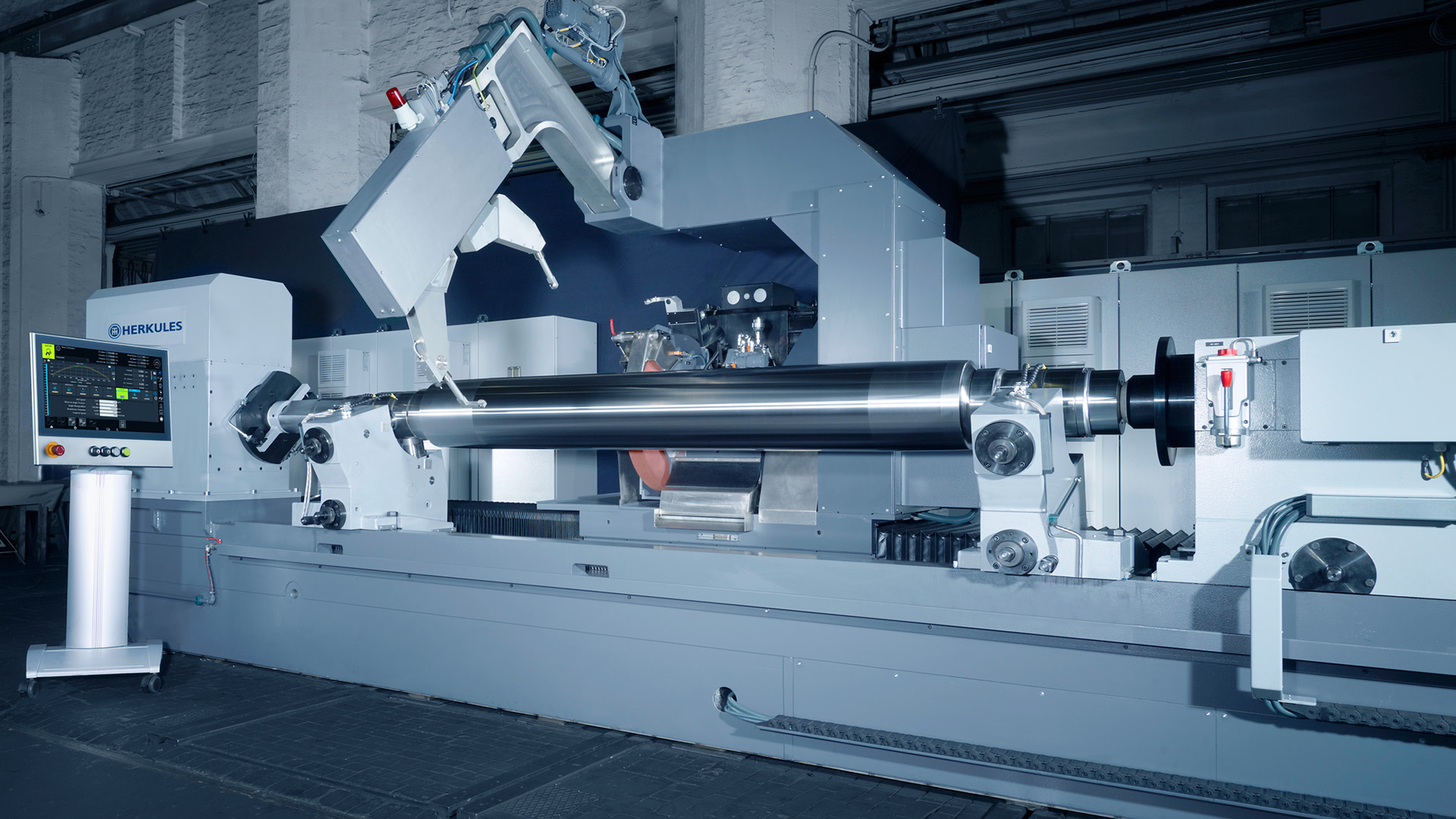
Perfect Rolls, The Very Best Foil
WS 450 AL Monolith™ for Hydro Aluminium Deutschland GmbH
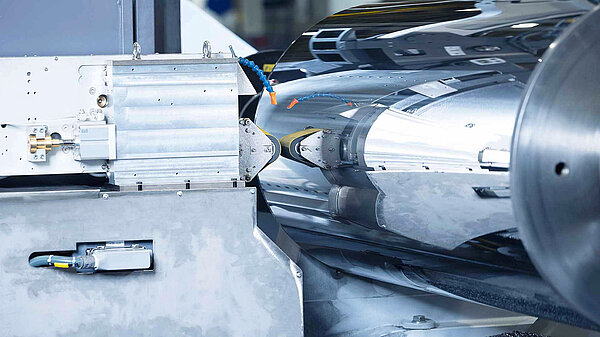
Absolutely accurate roll geometry, exceptional surface quality – the aluminum industry faces ever more demanding requirements. Mills meet these demands with Herkules machines. 90% of all rolls used in foil production are ground with Herkules roll grinders.
Hydro Aluminium Deutschland GmbH has relied on Herkules for many years. In summer 2014 it invested again in a WS 450 AL Monolith™ from the market leader. Hydro Aluminium is a leading global producer of aluminum foil with a thickness of 6 μm and lithography strip with thicknesses of 0.1 to 0.5 mm. The new machine is the fourth Herkules machine at Hydro Aluminium, after a WS 400 and two WS 300 CNC.
Herkules specialists equipped the WS 450 AL Monolith™ with several accessories. It has a HCC/KPM CNC control, developed especially for machining rolls, as well as a HCC/KPM roll measuring system. With its three measuring probes, the roll measuring system allows for highly accurate measuring of the roll geometry and for "correction on the fly". The machine is equipped with a roll surface inspection system (RSIS), which indicates even the minutest surface defects. The Monolith™ design of the grinder saves space and cost. It obviates the need for special machine foundations. It dramatically shortens installation time. The excellent damping characteristics of the vibration absorbing structure bring on a significant improvement in machining accuracy.
The optimal adaptation to the stringent requirements of the aluminum industry makes for accurate and efficient machining – a cornerstone of the customer's competitiveness.