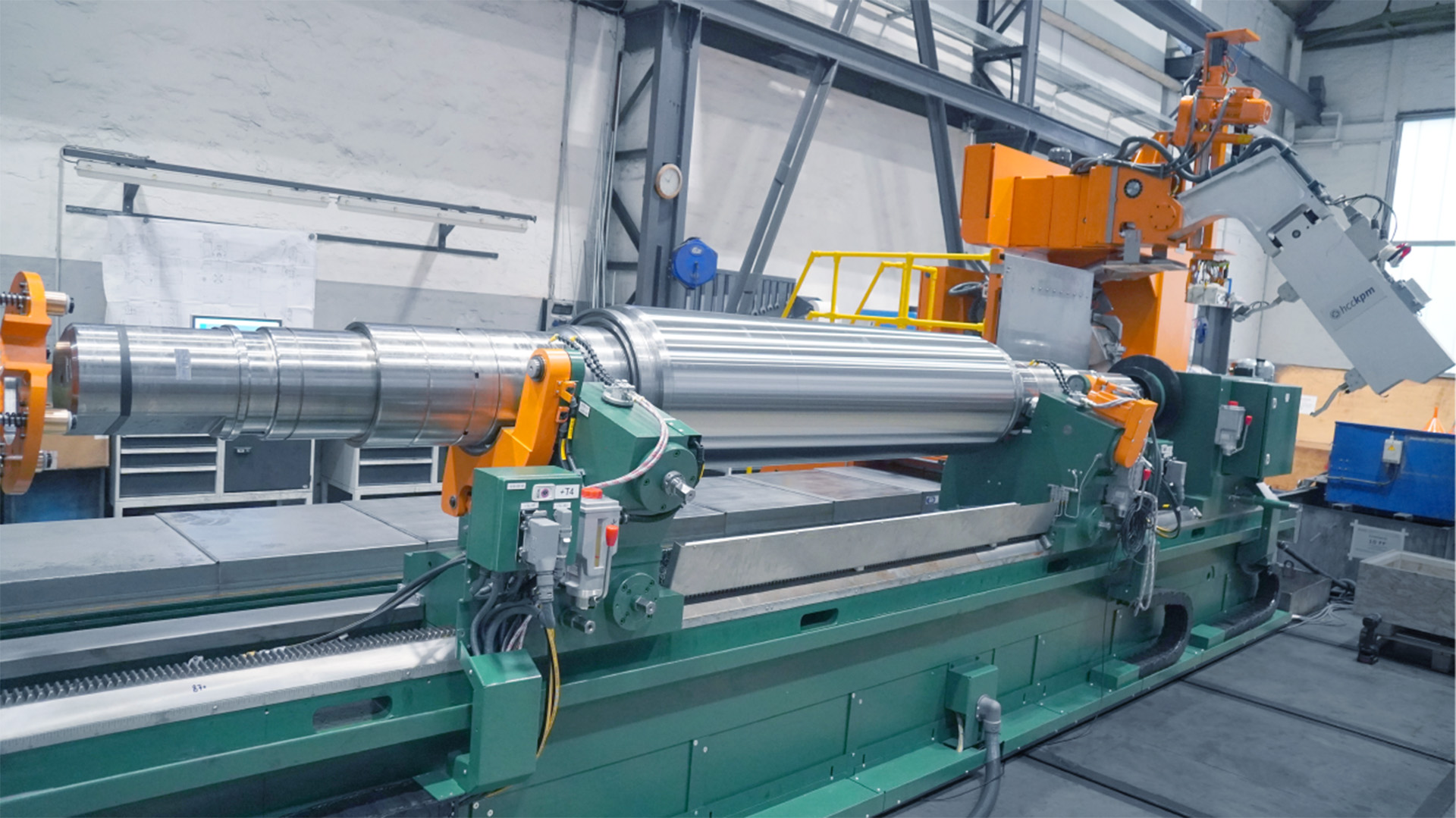
Maximum Geometric Precision for Spanish Cold Rolling Mill
For a greenfield project with a Roll Shop in the new cold rolling mill near León (located directly on the famous Way of St. James), Coated Solutions, a Spanish producer of color-coated or pre-painted steel strip, decided to purchase a foundation-free WS 450 S × 4500 CNC Monolith™ roll grinder for machining back-up and work rolls with a grinding diameter of up to 1,200 mm.
To ensure the geometric precision of the roll, the machine is equipped with our reliable inspection technology for crack detection using Eddy Current and Ultrasonic measurement with Creeping Wave. The Eddy Current sensor detects cracks on the roll surface, while the Ultrasonic sensor also detects defects both close to the roll surface and deep inside the roll core.
In addition, the grinding machine is equipped with an integrated measuring device for measuring the roll geometry and alignment. The measuring probe thus provides an exact image of the current grinding condition on the workpiece. The resulting measurement data in real time can then be used for compensation grinding and can be subsequently processed by our Roll Shop Management System.
For the inspection, mounting, and removal of the roll chocks, two pullers and a chock tilter are also included in the Herkules scope of delivery, enabling the Roll Shop to be operated safely and efficiently.
The assembly is carried out, monitored and approved by our experts on site.
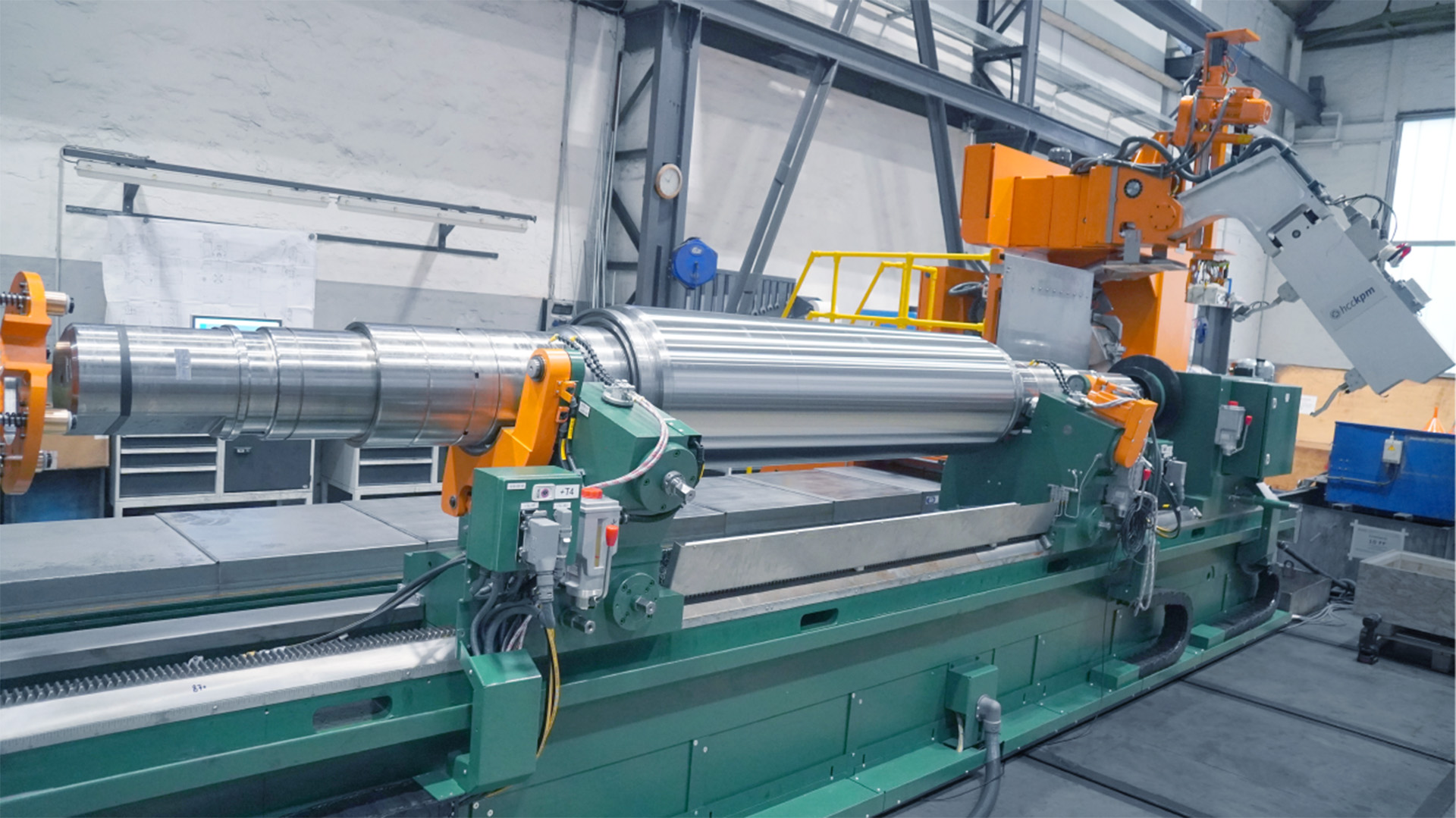
Maximum Geometric Precision for Spanish Cold Rolling Mill
For a greenfield project with a Roll Shop in the new cold rolling mill near León (located directly on the famous Way of St. James), Coated Solutions, a Spanish producer of color-coated or pre-painted steel strip, decided to purchase a foundation-free WS 450 S × 4500 CNC Monolith™ roll grinder for machining back-up and work rolls with a grinding diameter of up to 1,200 mm.
To ensure the geometric precision of the roll, the machine is equipped with our reliable inspection technology for crack detection using Eddy Current and Ultrasonic measurement with Creeping Wave. The Eddy Current sensor detects cracks on the roll surface, while the Ultrasonic sensor also detects defects both close to the roll surface and deep inside the roll core.
In addition, the grinding machine is equipped with an integrated measuring device for measuring the roll geometry and alignment. The measuring probe thus provides an exact image of the current grinding condition on the workpiece. The resulting measurement data in real time can then be used for compensation grinding and can be subsequently processed by our Roll Shop Management System.
For the inspection, mounting, and removal of the roll chocks, two pullers and a chock tilter are also included in the Herkules scope of delivery, enabling the Roll Shop to be operated safely and efficiently.
The assembly is carried out, monitored and approved by our experts on site.
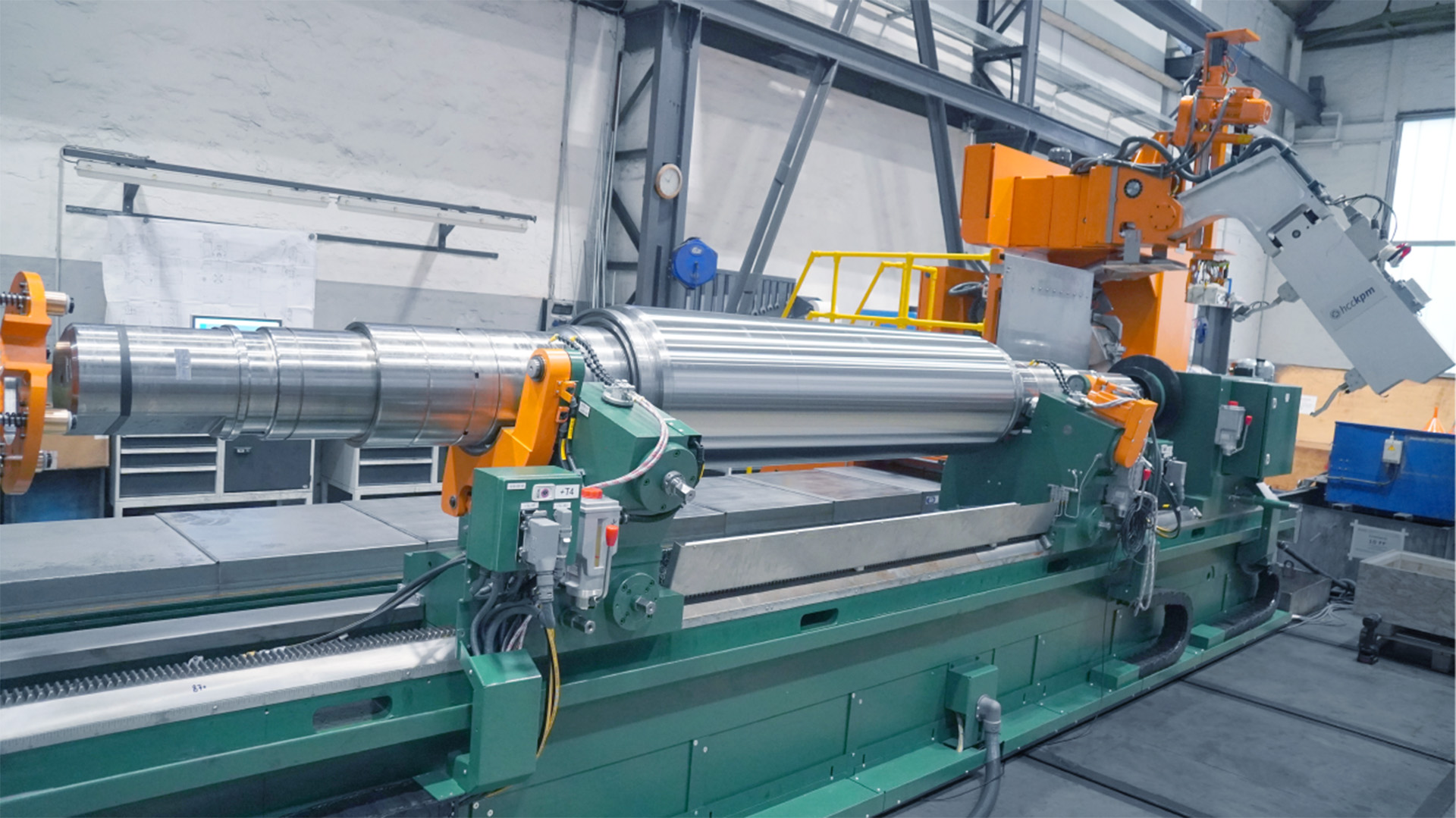
Maximum Geometric Precision for Spanish Cold Rolling Mill
For a greenfield project with a Roll Shop in the new cold rolling mill near León (located directly on the famous Way of St. James), Coated Solutions, a Spanish producer of color-coated or pre-painted steel strip, decided to purchase a foundation-free WS 450 S × 4500 CNC Monolith™ roll grinder for machining back-up and work rolls with a grinding diameter of up to 1,200 mm.
To ensure the geometric precision of the roll, the machine is equipped with our reliable inspection technology for crack detection using Eddy Current and Ultrasonic measurement with Creeping Wave. The Eddy Current sensor detects cracks on the roll surface, while the Ultrasonic sensor also detects defects both close to the roll surface and deep inside the roll core.
In addition, the grinding machine is equipped with an integrated measuring device for measuring the roll geometry and alignment. The measuring probe thus provides an exact image of the current grinding condition on the workpiece. The resulting measurement data in real time can then be used for compensation grinding and can be subsequently processed by our Roll Shop Management System.
For the inspection, mounting, and removal of the roll chocks, two pullers and a chock tilter are also included in the Herkules scope of delivery, enabling the Roll Shop to be operated safely and efficiently.
The assembly is carried out, monitored and approved by our experts on site.
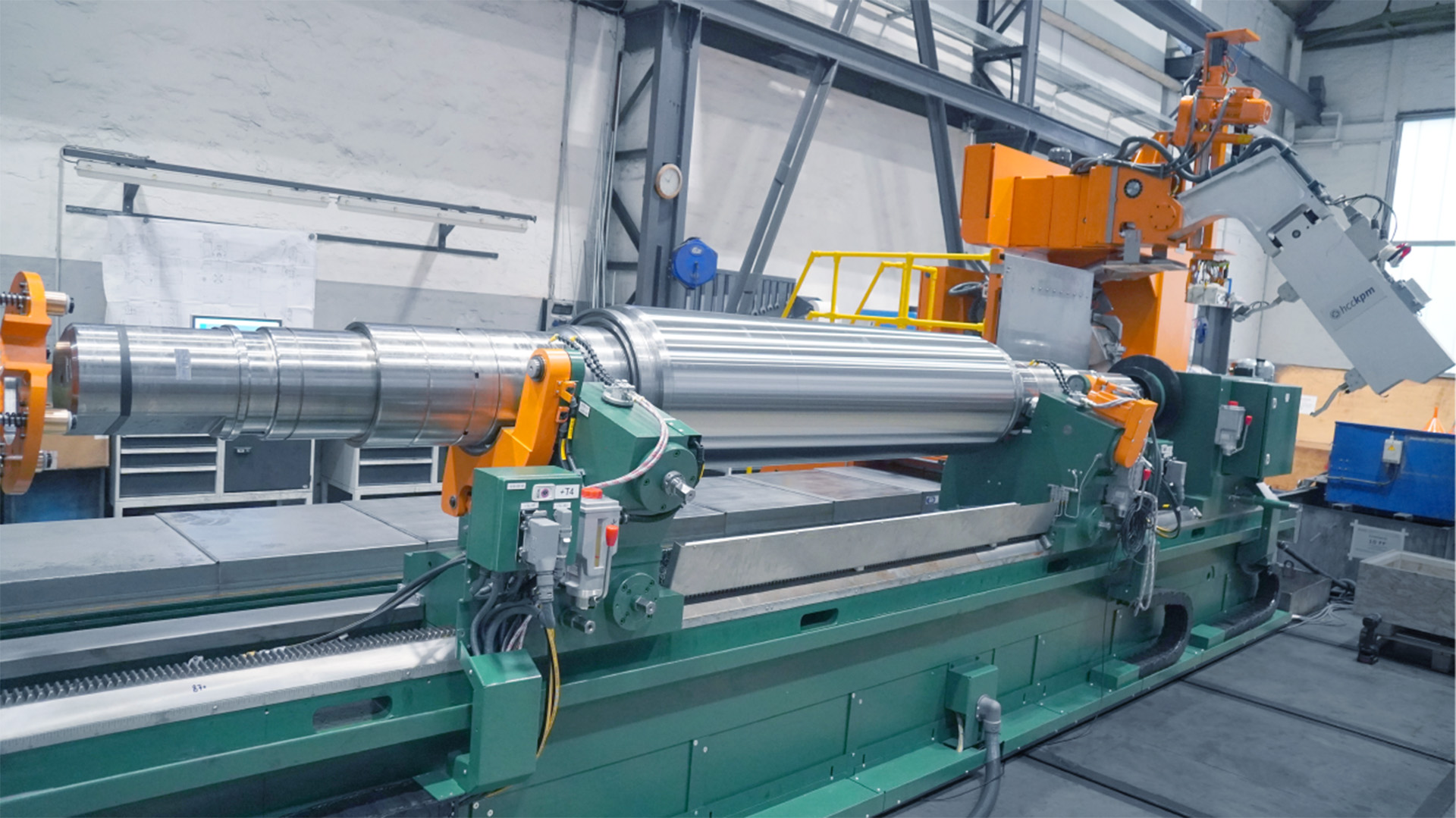
Maximum Geometric Precision for Spanish Cold Rolling Mill
For a greenfield project with a Roll Shop in the new cold rolling mill near León (located directly on the famous Way of St. James), Coated Solutions, a Spanish producer of color-coated or pre-painted steel strip, decided to purchase a foundation-free WS 450 S × 4500 CNC Monolith™ roll grinder for machining back-up and work rolls with a grinding diameter of up to 1,200 mm.
To ensure the geometric precision of the roll, the machine is equipped with our reliable inspection technology for crack detection using Eddy Current and Ultrasonic measurement with Creeping Wave. The Eddy Current sensor detects cracks on the roll surface, while the Ultrasonic sensor also detects defects both close to the roll surface and deep inside the roll core.
In addition, the grinding machine is equipped with an integrated measuring device for measuring the roll geometry and alignment. The measuring probe thus provides an exact image of the current grinding condition on the workpiece. The resulting measurement data in real time can then be used for compensation grinding and can be subsequently processed by our Roll Shop Management System.
For the inspection, mounting, and removal of the roll chocks, two pullers and a chock tilter are also included in the Herkules scope of delivery, enabling the Roll Shop to be operated safely and efficiently.
The assembly is carried out, monitored and approved by our experts on site.