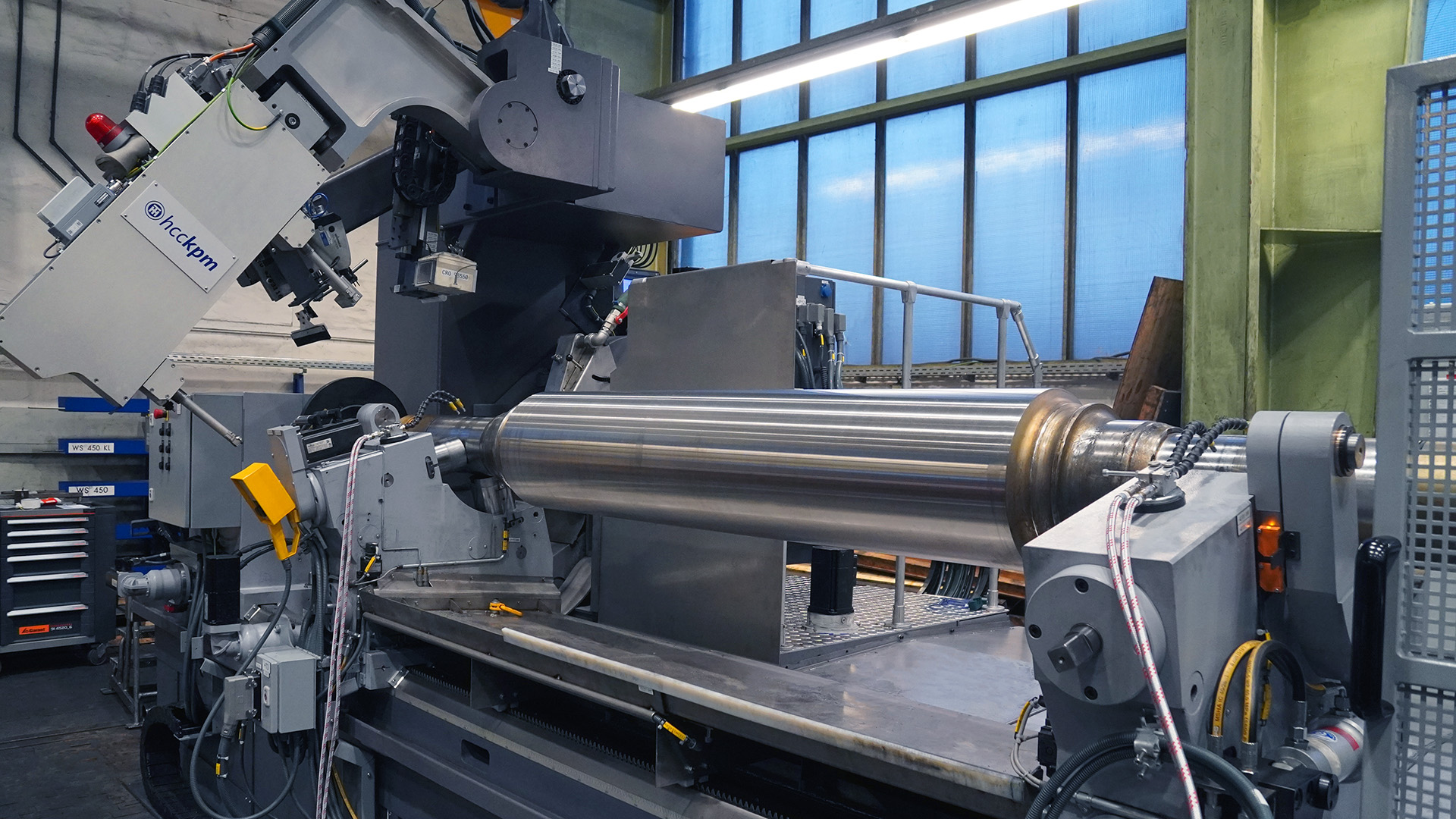
Highest Machine Accuracies - Flawless Cold-Rolled Strip
With its newly acquired WS 450 x 4250 CNC Monolith™ roll grinding machine, a Japanese manufacturer of cold-rolled and coated steel sheets and coils as well as electrogalvanized electrical steel sheets reliably achieves first-class surfaces and geometries during roll machining in its cold rolling mill.
The foundation-free, highly automated machine is specially tailored to our customer's needs and equipped with a comprehensive range of accessories.
In order to achieve demanding CVC profiles and curve shapes of the work rolls considering the tightest manufacturing tolerances and highest surface accuracies, the machine is equipped with an additional B-axis. The advantages: Feed marks are avoided, material removal from the grinding wheel is optimized and grinding times are significantly reduced.
Reliable Measurement Data within Milliseconds
Thanks to HCC/KPM's fully integrated, intuitive machine control system, in which the entire processes of roll handling, machining and inspection are integrated, the highest machining quality is ensured at all times.
HCC/KPM's C-Frame calipers are highly accurate devices for roll measurement. Due to the compact and stable design with swiveling arms, the calipers can be used for very small as well as very large roll diameters. With the C-frame measuring technology, every type of roll is measured with high precision and reliability.
Together with the machine controls from HCC/KPM, the C-Frame caliper allows corrections "on the fly" during the grinding process. The result: maximum efficiency and high-precision ground rolls.
For automatic detection of surface defects on the roll, HCC/KPM offers the Roll Surface Inspection System (RSIS) laser measuring device. The RSIS detects the reflection of a laser beam on the roll surface and evaluates it. Processing defects such as chatter and feed marks, commas, clouds and similar defect patterns are thus reliably detected.
Acceptance of the machine took place at the Siegen site at the beginning of December./p>
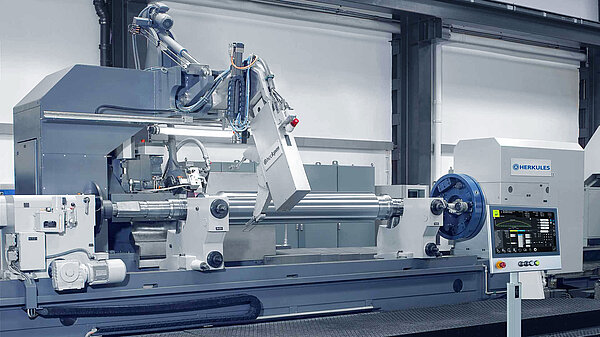
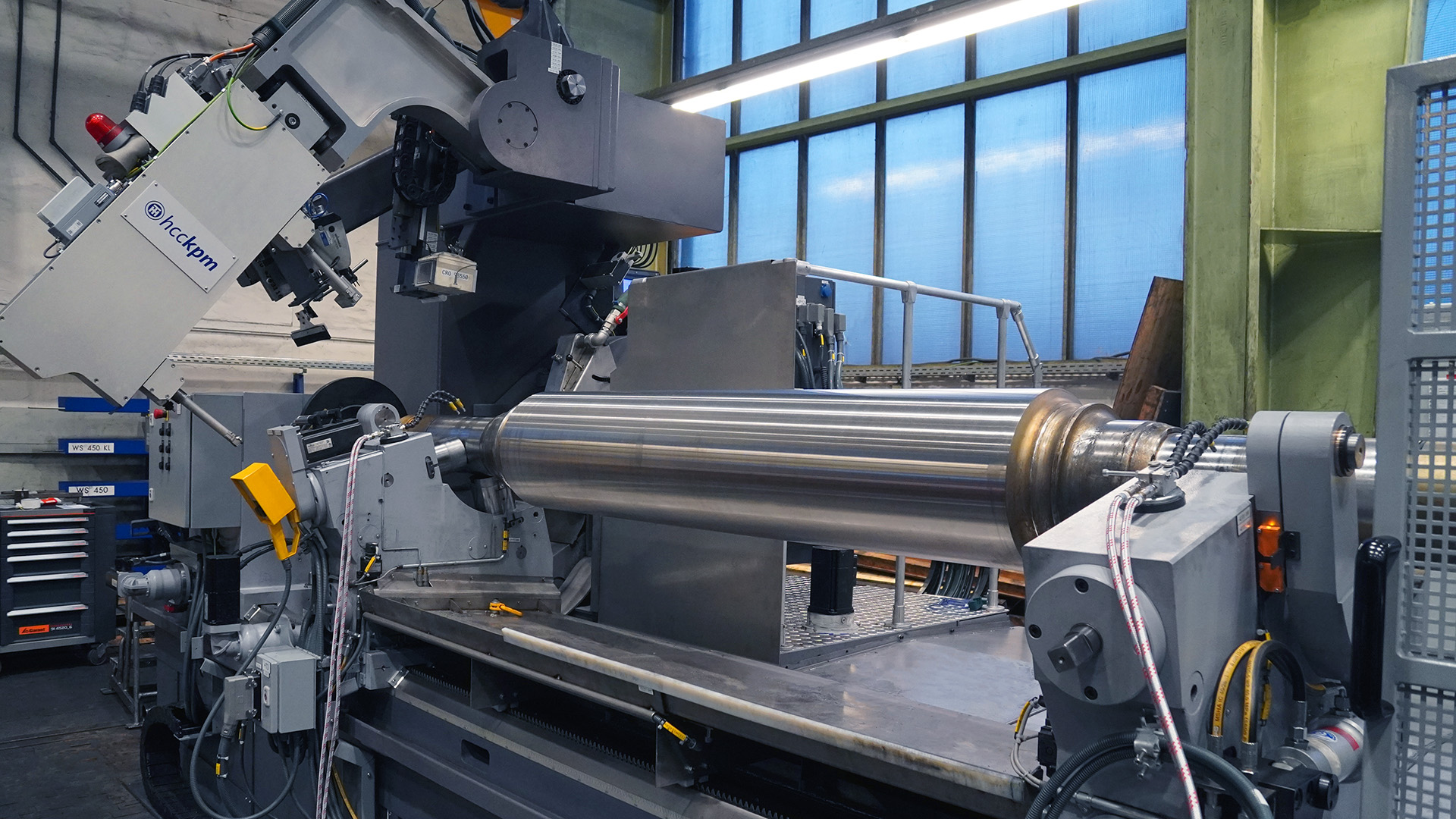
Highest Machine Accuracies - Flawless Cold-Rolled Strip
With its newly acquired WS 450 x 4250 CNC Monolith™ roll grinding machine, a Japanese manufacturer of cold-rolled and coated steel sheets and coils as well as electrogalvanized electrical steel sheets reliably achieves first-class surfaces and geometries during roll machining in its cold rolling mill.
The foundation-free, highly automated machine is specially tailored to our customer's needs and equipped with a comprehensive range of accessories.
In order to achieve demanding CVC profiles and curve shapes of the work rolls considering the tightest manufacturing tolerances and highest surface accuracies, the machine is equipped with an additional B-axis. The advantages: Feed marks are avoided, material removal from the grinding wheel is optimized and grinding times are significantly reduced.
Reliable Measurement Data within Milliseconds
Thanks to HCC/KPM's fully integrated, intuitive machine control system, in which the entire processes of roll handling, machining and inspection are integrated, the highest machining quality is ensured at all times.
HCC/KPM's C-Frame calipers are highly accurate devices for roll measurement. Due to the compact and stable design with swiveling arms, the calipers can be used for very small as well as very large roll diameters. With the C-frame measuring technology, every type of roll is measured with high precision and reliability.
Together with the machine controls from HCC/KPM, the C-Frame caliper allows corrections "on the fly" during the grinding process. The result: maximum efficiency and high-precision ground rolls.
For automatic detection of surface defects on the roll, HCC/KPM offers the Roll Surface Inspection System (RSIS) laser measuring device. The RSIS detects the reflection of a laser beam on the roll surface and evaluates it. Processing defects such as chatter and feed marks, commas, clouds and similar defect patterns are thus reliably detected.
Acceptance of the machine took place at the Siegen site at the beginning of December./p>
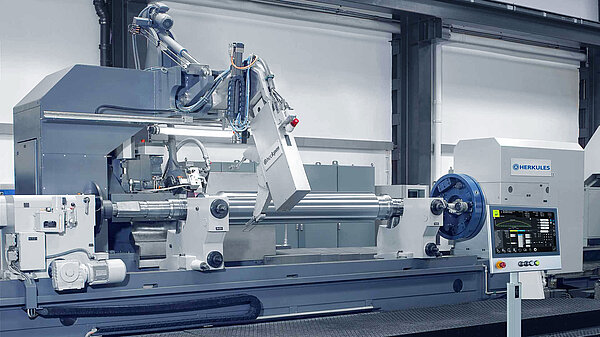