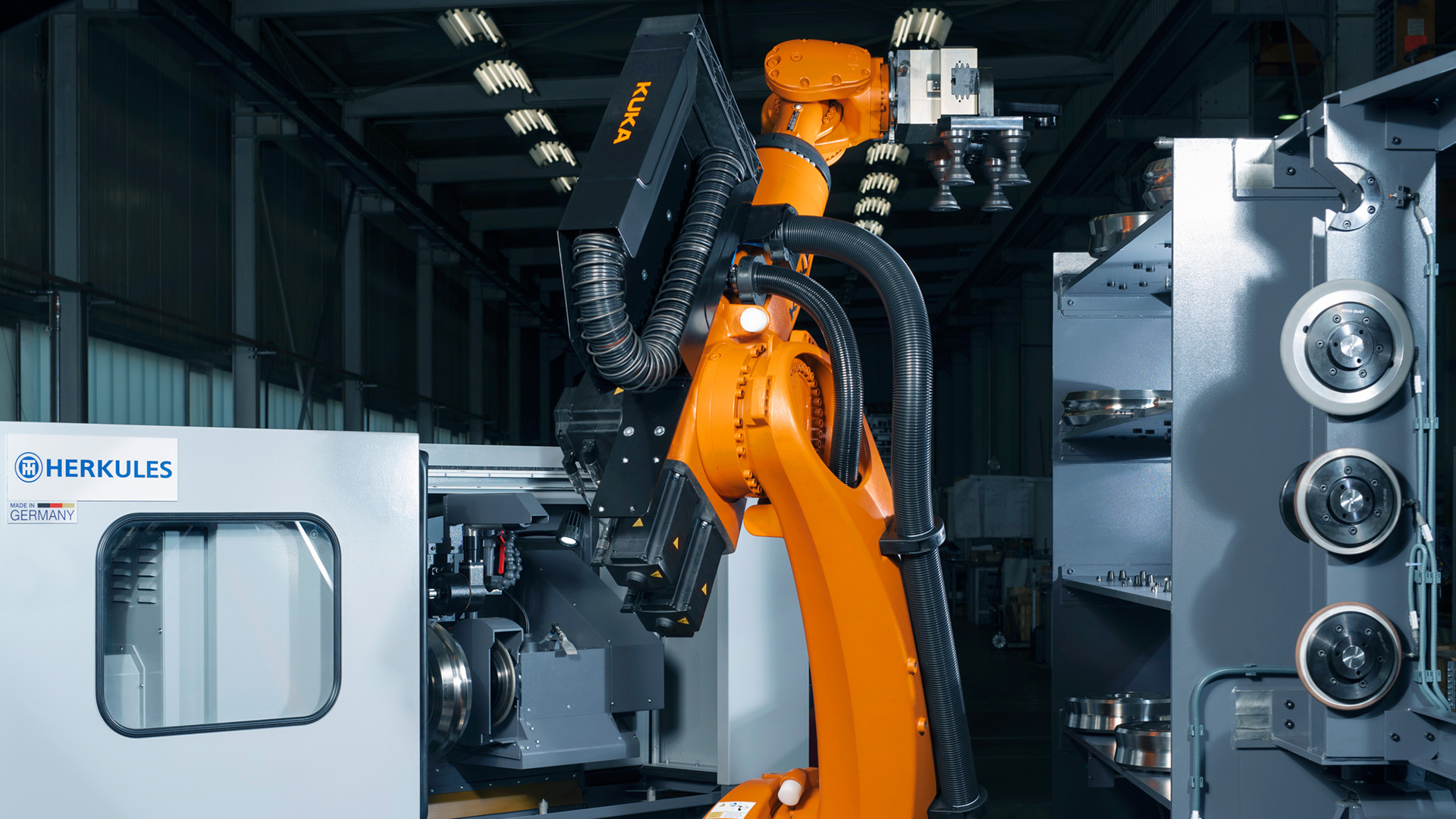
High-Degree Automation Solution
With an HS3 CNC groove grinder and a robot for automatic loading and unloading of the roll rings, the Chinese Baoshan Co., Ltd., one of the largest steel companies in the world, has awarded a contract for a project with a hitherto unprecedented degree of automation.
Almost all work processes will be fully automated in the future: In addition to the loading of the roll rings, the groove grinder is equipped with a grinding wheel changing system. The transfer of roll rings between the roll shop and the machine is carried out by automated transfer cars. The rings are removed fully automatically from specially manufactured rack systems, each with 19 spaces, clamped in the machine and then replaced with unground rings after completion of the grinding process.
The highly efficient machine concept was developed and implemented in detail according to the customer’s ideas. For this purpose, the loading robot was also integrated into HCC/KPM’s KP 20 control system, which was specially developed for groove grinding. Direct communication between the robot, machine and transfer car is provided by a Manufacturing Executive System (MES system) from HCC/KPM. This significantly shortens the machining times of the roll rings and guarantees first-class grinding results.
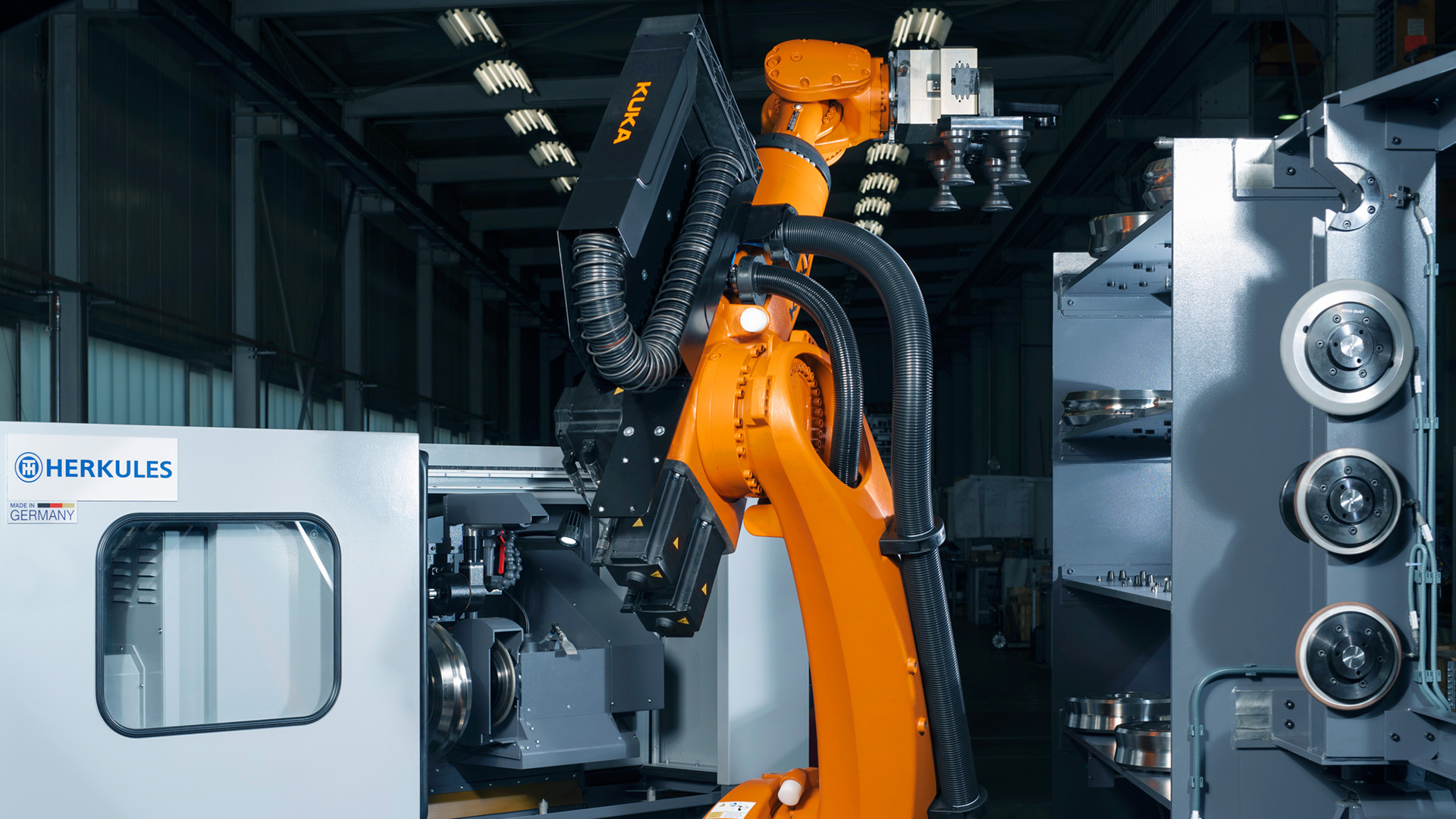
High-Degree Automation Solution
With an HS3 CNC groove grinder and a robot for automatic loading and unloading of the roll rings, the Chinese Baoshan Co., Ltd., one of the largest steel companies in the world, has awarded a contract for a project with a hitherto unprecedented degree of automation.
Almost all work processes will be fully automated in the future: In addition to the loading of the roll rings, the groove grinder is equipped with a grinding wheel changing system. The transfer of roll rings between the roll shop and the machine is carried out by automated transfer cars. The rings are removed fully automatically from specially manufactured rack systems, each with 19 spaces, clamped in the machine and then replaced with unground rings after completion of the grinding process.
The highly efficient machine concept was developed and implemented in detail according to the customer’s ideas. For this purpose, the loading robot was also integrated into HCC/KPM’s KP 20 control system, which was specially developed for groove grinding. Direct communication between the robot, machine and transfer car is provided by a Manufacturing Executive System (MES system) from HCC/KPM. This significantly shortens the machining times of the roll rings and guarantees first-class grinding results.
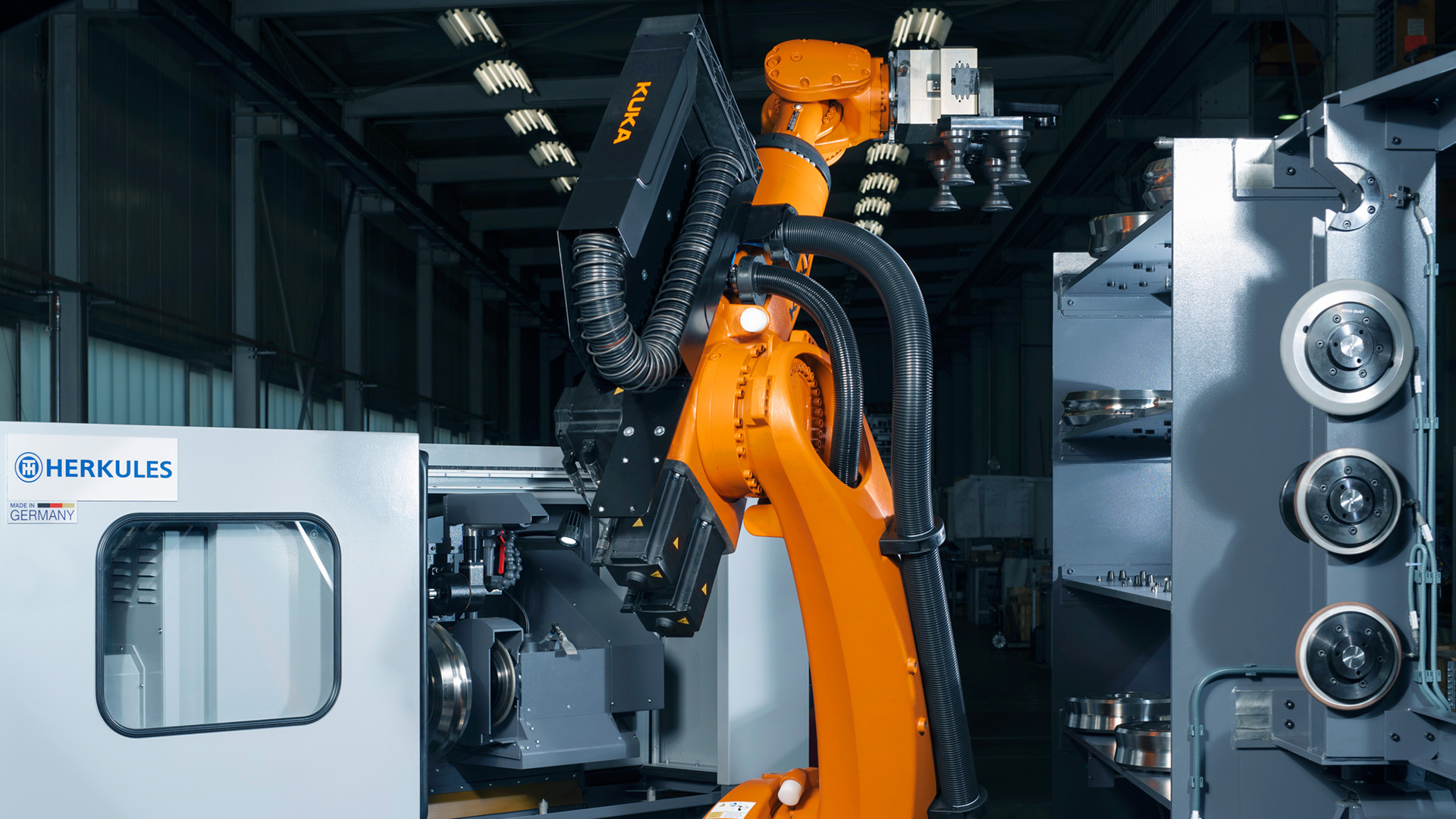
High-Degree Automation Solution
With an HS3 CNC groove grinder and a robot for automatic loading and unloading of the roll rings, the Chinese Baoshan Co., Ltd., one of the largest steel companies in the world, has awarded a contract for a project with a hitherto unprecedented degree of automation.
Almost all work processes will be fully automated in the future: In addition to the loading of the roll rings, the groove grinder is equipped with a grinding wheel changing system. The transfer of roll rings between the roll shop and the machine is carried out by automated transfer cars. The rings are removed fully automatically from specially manufactured rack systems, each with 19 spaces, clamped in the machine and then replaced with unground rings after completion of the grinding process.
The highly efficient machine concept was developed and implemented in detail according to the customer’s ideas. For this purpose, the loading robot was also integrated into HCC/KPM’s KP 20 control system, which was specially developed for groove grinding. Direct communication between the robot, machine and transfer car is provided by a Manufacturing Executive System (MES system) from HCC/KPM. This significantly shortens the machining times of the roll rings and guarantees first-class grinding results.
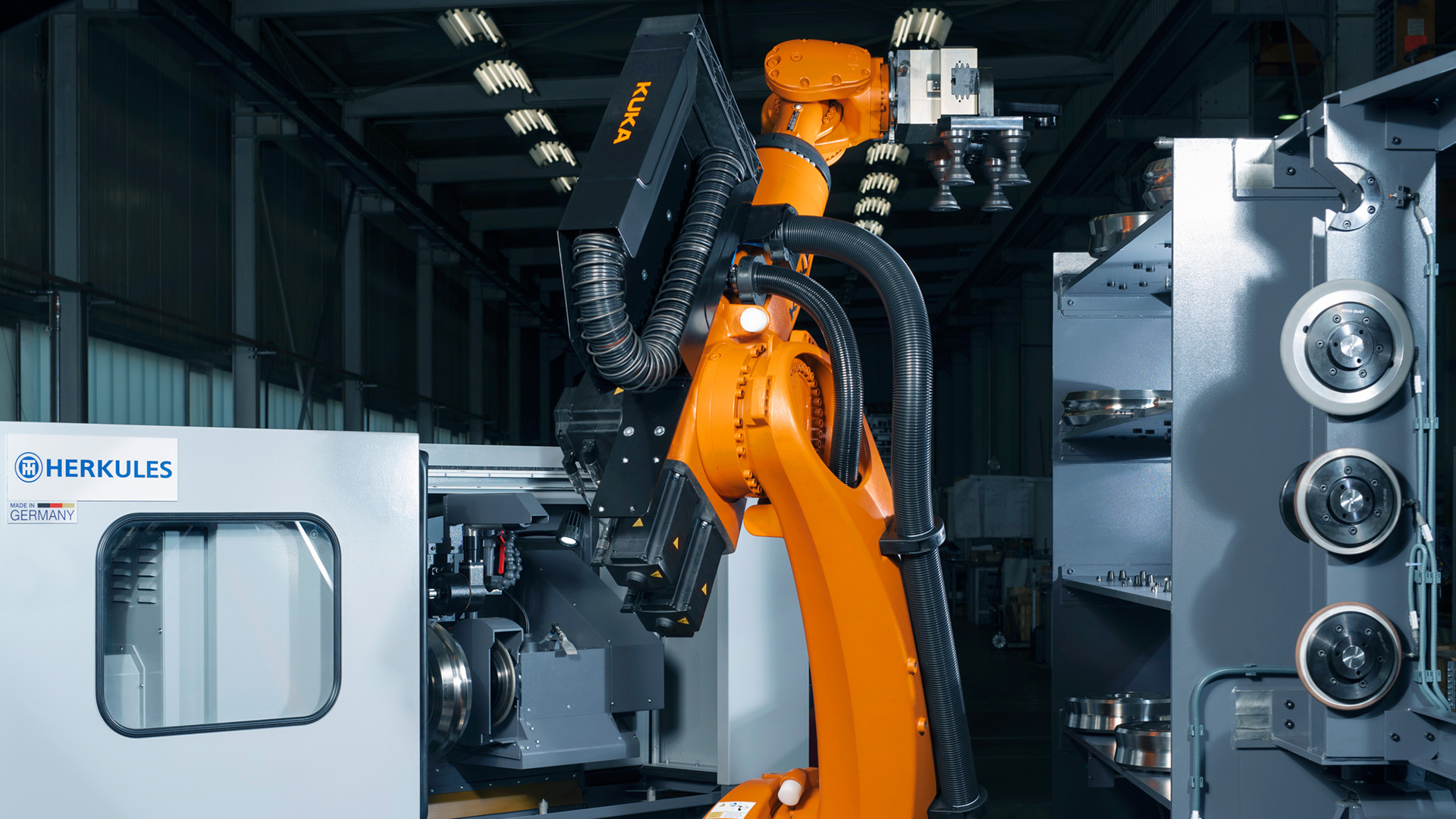
High-Degree Automation Solution
With an HS3 CNC groove grinder and a robot for automatic loading and unloading of the roll rings, the Chinese Baoshan Co., Ltd., one of the largest steel companies in the world, has awarded a contract for a project with a hitherto unprecedented degree of automation.
Almost all work processes will be fully automated in the future: In addition to the loading of the roll rings, the groove grinder is equipped with a grinding wheel changing system. The transfer of roll rings between the roll shop and the machine is carried out by automated transfer cars. The rings are removed fully automatically from specially manufactured rack systems, each with 19 spaces, clamped in the machine and then replaced with unground rings after completion of the grinding process.
The highly efficient machine concept was developed and implemented in detail according to the customer’s ideas. For this purpose, the loading robot was also integrated into HCC/KPM’s KP 20 control system, which was specially developed for groove grinding. Direct communication between the robot, machine and transfer car is provided by a Manufacturing Executive System (MES system) from HCC/KPM. This significantly shortens the machining times of the roll rings and guarantees first-class grinding results.