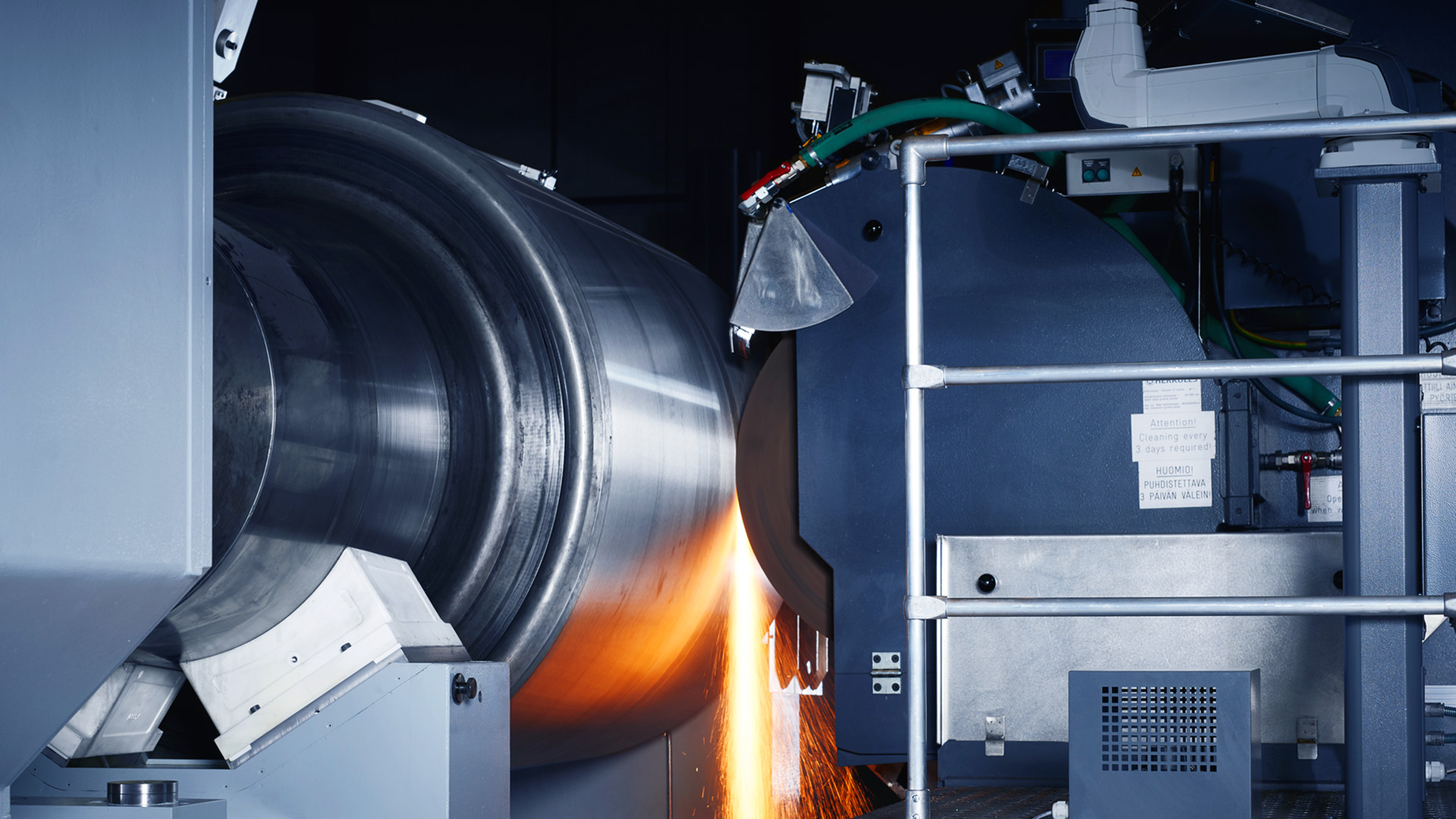
Perfect Grinding Results in the XXL Range
Monolith™ Machines for the Entire Roll Spectrum
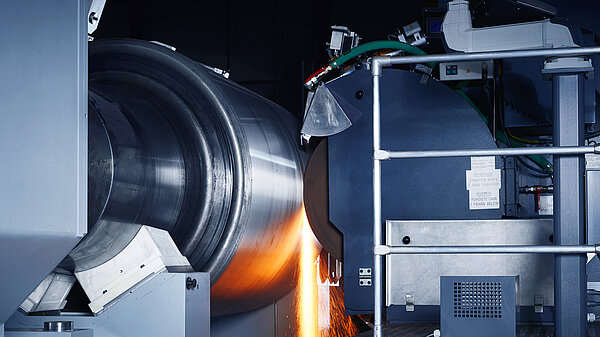
The history of success of the Monolith™ technology started 16 years ago, but it constantly adds new chapters. Grinding heaviest rolls in chocks is one of the current challenges that can be solved with the foundation-free sandwich design, saving space and investment cost.
A roll grinder of the type WS 1100 Monolith™ has just taken up operation at Outokumpu Oy. It grinds rolls with mounted chocks with weights of up to 90 t. Before commissioning in Finland, Herkules invited customers to attend its Open House on February 16. Here, the visitors witnessed the machine’s advantages during a live demonstration: excellent grinding results thanks to high stiffness and outstanding damping characteristics in a foundation-free design that saves space and money.
Significantly enhanced stiffness in comparison to machines with a classic foundation
The superiority of Monolith™ beds in comparison to conventional machine beds in terms of stability and vibration behavior has been proven by research conducted by the Laboratory for Machine Tools and Production Engineering (WZL) of RWTH Aachen University: direct comparative measurements of a classic roll grinder and a roll grinder with a Monolith™ machine bed have shown that the stiffness of the latter is twice as high. Moreover, the factor is as high as 5 regarding the dynamic stiffness. These results have been confirmed by decades of on-the-job experience: Monolith™ beds provide better grinding results. More than 200 roll grinders in Monolith™ sandwich design have been sold to customers around the world since 2001 – the anniversary machine recently went to Shandong Yuanrui Metal Material in China. The application area ranges from Sendzimir rolls with diameters of just a few centimeters to heavy plate mill rolls.