Automatic Machining Center
The Highest Level of Productivity
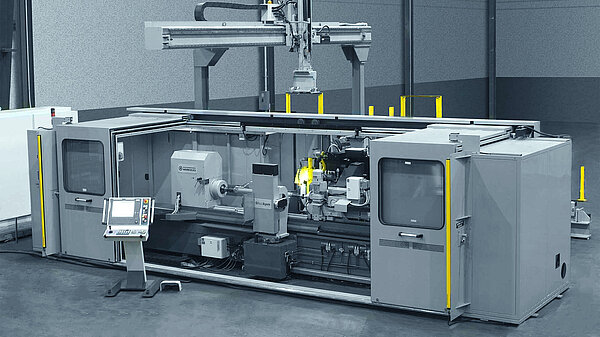
A fully automated machining center with two roll grinders, an integrated loading device and a small set-up area – Herkules developed this pioneering solution for a customer in the stainless steel industry. The machine loader concept was designed to guarantee highestquality machining results "made by Herkules" and maximum productivity, thanks to the automatic loading and unloading of workpieces, including transport to and from the roll pallet.
The core components of the compact machining center are two roll grinders of the type WS 250 Monolith™. It is loaded via a traversing workpiece pallet which can be parked within and outside of the fully automated area. While the workpieces of one pallet are machined, the other pallet is loaded and unloaded. Thus, non-productive time is reduced and the capacity is increased – valuable production time of the grinders is wasted no longer.
Compact design for a minimum of required space
The cross-system control regulates the smooth workflow between the machines and the loading device and allows for fully automated machining of all workpieces on the pallet, one after the other, in one single program. The loader is designed for the transport of two rolls (the roll which has just been ground and the one to be ground next) at the same time. Thus, empty runs to collect and take away workpieces are minimized. Thanks to the compact design, travel distances of the loader are short and the whole machining center requires a comparatively small set-up area.
Both machines feature the well known and unique Monolith™ beds that do not require a foundation. The loading device does not require a foundation either. On the one hand, this is an interesting fi nancial aspect of the loader concept; on the other, it means that the production process is not disturbed by foundation works which would otherwise be necessary.
New driver concept
The rolls are taken up between centers. In order to avoid having to equip them with an additional driver, Herkules has developed a system which automatically engages and drives the rolls with the help of driving pins. The forces developing during the grinding process are compensated by a fully automated one-point steady rest. The steady rest runs parallel to the grinding wheel and guarantees the highest shaping accuracy and surface quality of the workpieces, long-term and reproducibly. The machining center is able to machine up to 3,500 rolls per month with a roughness of Ra 0.10 μm.
The new machining center unites the highest machining quality and precision of Herkules roll grinders with maximum productivity. Two machining centers went into operation in a stainless steel plant in 2012 already. The quality requirements in the specifi cation catalogue were high – they were, however, even exceeded by Herkules, to the full satisfaction of the customer.